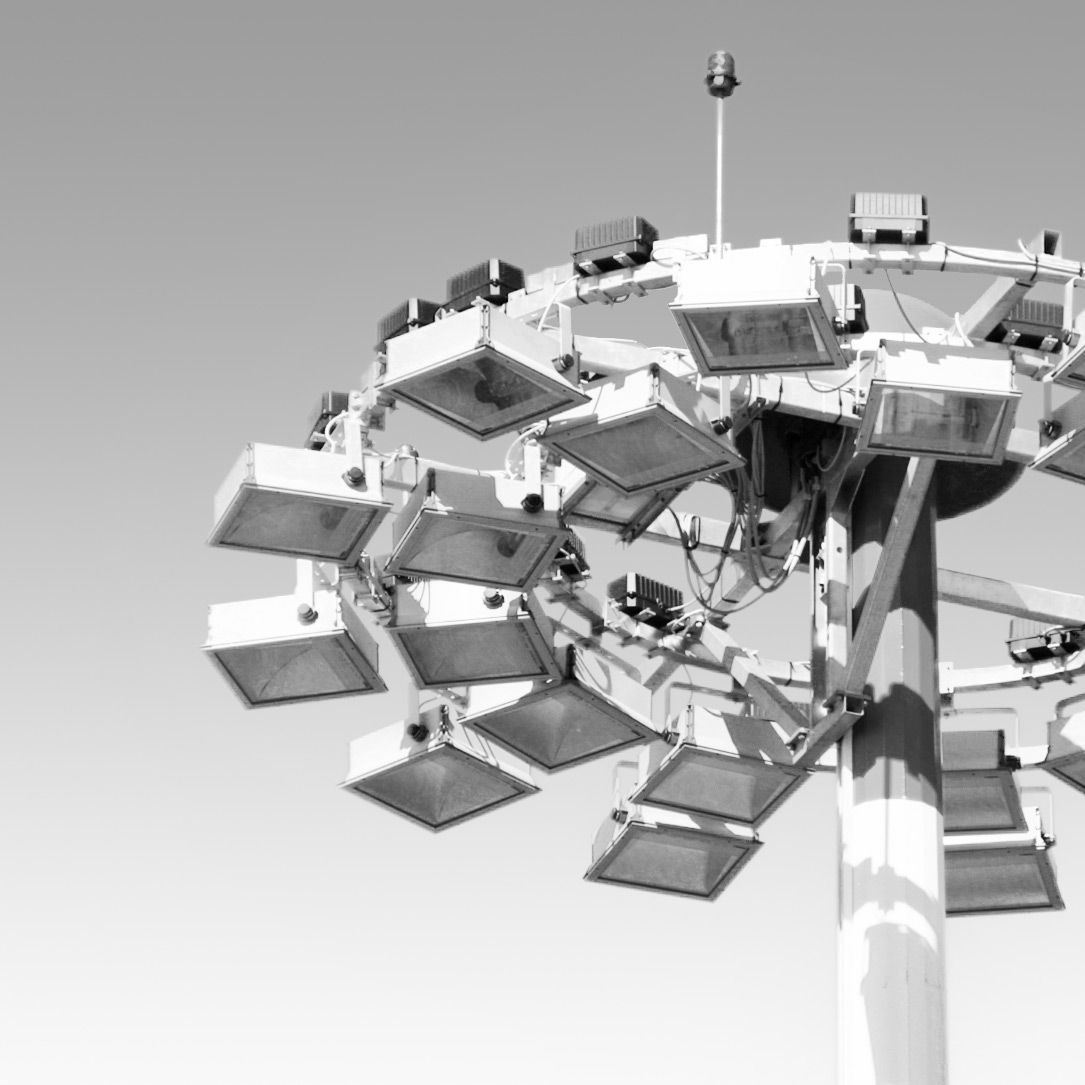
Products
High masts:
safety is standard.
In this page…
N.C.M. High Masts
Movable under the most extreme wind conditions, N.C.M. high masts offer unique management possibilities, combined with the multiservice system available for the implementation and concentration of various functionalities, from lighting to signal distribution.
Equipped with built-in safety systems, they represent the state of the art in N.C.M. production.
Product Categories
Ideal for sports facilities of all sizes and large open areas, these structures represent a versatile and cost-effective solution.
They are truncated cone-shaped with a polygonal section and are made of S355JR steel sheet (according to UNI EN 10025 standard), using press-bending followed by longitudinal welding. They are composed of multiple sections, assembled using the slip-on joint method.
The high masts can be:
- embedded directly into a concrete foundation block
- anchored to the foundation using bolts embedded in it, in the case they are equipped with a base plate welded to the bottom section of the shaft.
Welds are performed using a procedure certified by the Italian Welding Institute, by qualified personnel, and tested in accordance with UNI EN 3834-2 standard.
Each high mast is equipped with one of the following types of climbing ladder:
- modular arched ladder with safety guardrail
- ladder with central “T”-shaped guide, to be used with a CE-certified fall arrest device.
The modular ladder is installed on the back side of the lighting face and is fixed to the mast with welded supports.
At the top of the tower, there is a platform sized according to the number of floodlights installed.
The platform, accessed via a hatch on the walking surface, allows for safe maintenance of the floodlights.
The mast is also equipped with a number of resting balconies, varying based on the height of the pole, attached with welded supports.
In towers equipped with T-type ladders, resting platforms are supplied instead.
All structures are CE marked and manufactured in accordance with UNI EN 1090, execution class EXC 2.
The high masts are hot-dip galvanized by immersion in a zinc bath, in compliance with UNI EN ISO 1461.
Upon customer request, polyester powder coating is available, carried out according to UNI EN ISO 2409, class 1-2808 – DIN 53132 – ASTM B117.
These are an excellent lighting solution for roundabouts, parking areas, or green spaces that do not require a large number of floodlights.
They feature a truncated cone shape with a polygonal section and are made from S355JR steel sheet (according to UNI EN 10025 standard) through press-bending and longitudinal welding.
They are composed of multiple sections—depending on the tower’s height—joined together using the slip-on joint method.
The base section of the mast houses the winch system, reinforced to restore the original flexural strength of the structure.
The high masts can be:
- directly embedded into a concrete foundation block.
- anchored to the foundation via anchor bolts, if equipped with a base plate welded to the bottom section of the shaft.
Welds are performed using a certified procedure from the Italian Welding Institute, by qualified personnel, and tested in compliance with UNI EN 3834-2.
MANUAL MOBILE SYSTEM WITH GUIDED CROWN
– MAST HEAD
Located at the top of the pole, the mast head houses the pulley system mounted on sealed bearings.
It also includes:
- a mechanical locking device for the floodlight crown in its working position, designed to release the cable from bearing the crown’s weight.
- anti-rotation centering pins to counter wind forces acting on the floodlight crown.
– FLOODLIGHT CROWN
The mobile crown, made of steel profiles and designed to support the floodlights, is fixed to the trolley.
– TROLLEY
The trolley enables the vertical movement of the crown and is equipped with the exclusive NCM parachute brake, which activates in case of cable slack.
Thanks to polyamide sliders, the trolley moves within a lightweight alloy guide fixed along the mast, allowing smooth movement even in windy conditions.
The mechanical locking to the mast head is ensured by two steel spring plates, which relieve the cable of the crown’s weight when in static working position.
– CABLE
The cable is made from high-strength galvanized steel wires; it is very flexible and highly resistant to surface corrosion (with a safety factor greater than 5).
One end is fixed to the trolley, while the other is wound around the winch drum located inside the shaft, accessible through an inspection hatch.
– WINCH
The crown is operated via a manual winch equipped with an automatic friction brake.
– ELECTRICAL ACCESSORIES
The mast’s power line can be disconnected internally using a fused lock switch located at the inspection hatch.
Floodlights are powered by a multipolar cable fixed inside the mast. At the top, it connects to a 6-pole plug/socket unit, while at the bottom it is connected to the lock switch via a socket.
– MAST COVER
A fiberglass dome is mounted at the top of the mast to protect the mechanical and electrical components.
The high masts are hot-dip galvanized by immersion in a zinc bath in accordance with UNI EN ISO 1461.
On request, polyester powder coating is available, carried out in compliance with UNI EN ISO 2409, class 1-2808 – DIN 53132 – ASTM B117.
They represent the top of the range in terms of technology and safety. They are mainly used for lighting large areas, such as ports and airports.
The lighting towers consist of a truncated conical shaft, made of one or more polygonal-section segments, manufactured from S355JR steel sheets (UNI EN10025 standard) by press bending and subsequent longitudinal welding of trapezoid-shaped sheets.
They are composed of multiple segments, the number of which depends on the height of the tower, joined using the slip-on joint method.
The base segment of the tower houses the winch for raising the crown/panel and the electrical equipment. This section is properly reinforced to restore the original bending resistance of the structure.
The shaft is designed to support the weight of the floodlights under operating conditions, taking into account the environmental characteristics of the installation area.
The lighting towers can be:
- Embedded directly into a concrete foundation base;
- Anchored to the foundation using embedded bolts, in case they are equipped with a base plate welded to the bottom segment of the shaft.
The welds are carried out using a certified procedure by the Italian Welding Institute, performed by qualified personnel and tested in accordance with UNI EN 3834-2 standards.
Mobile Crown System-
TOP OF THE POLE: Positioned at the top of the pole, it houses the return pulley for the cable. The following components are also installed:
- Mechanical locking device for the floodlight crown in working position, which unloads the weight of the crown and the floodlights from the cable;
- Anti-rotation centering pins, to counteract wind action on the lighting fixtures;
- Socket/plug body, which provides an electrical connection while keeping the power cables fixed inside the pole.
CROWN-PANEL FOR FLOODLIGHTS: Circular or rectangular in shape, made of steel profiles, fixed to the trolley and sized to support the lighting fixtures and their respective electrical components.
TROLLEY: Made of steel, it slides inside a lightweight alloy guide mounted along the shaft, allowing movement even in windy conditions. It is equipped with the exclusive NCM parachute brake, which activates in case of cable loosening. The sliding system uses friction-reducing polyamide devices.
The mechanical coupling to the pole head is automatic and performed through two spring-steel blades, which release the cable from the load in the static working position.
PARACHUTE BRAKE: A patented NCM safety device, located in the center of the trolley. It consists of a toothed lever that acts as a brake under the action of a pressure spring.
TRACTION CABLE: Made of high-tensile galvanized steel, or AISI 316 stainless steel for highly corrosive environments. It is sized based on the total weight to be lifted and has a safety factor equal to or greater than 5 in compliance with Machinery Directive 2006/42/EC.
DRIVE UNIT: Consists of a worm gear reducer combined with a preliminary gear stage, driven by a fixed or removable electric motor.
It is connected to a drum that moves the system by winding/unwinding the cable.
Depending on the load of the crown, the drive unit can be mounted on the shaft using a tilting support or integrated into a monoblock system. Both solutions include devices to continuously monitor cable tension.
MOTOR: The reducer is driven by an electric motor with power ranging from 0.75 to 1.5 kW – 3 phase – 50 Hz – 4 poles, powered at 380 V, based on the load applied to the crown. It comes with an electric control panel and a push-button panel for automatic crown engagement/release operations, along with a power cable of adequate length for safe-distance operation during movement.
The control panel includes line stop, up, and down commands. The motor is powered by the floodlight circuit.
This system allows movement and maintenance of floodlights simultaneously on multiple towers.
ELECTRICAL ACCESSORIES: The lamp power supply line is implemented with a fixed cable inside the tower and can be disconnected via a fused socket. The number of conductors depends on the number of independent circuits required. The cable runs from the socket, located in the winch compartment, and reaches the top of the tower, where it connects either directly to a female socket or to a junction box in case of prewired plug-socket systems.
A device at the base prevents connections from being made under voltage.
PROTECTIVE DOME: The electrical and coupling components at the top are protected by a fiberglass dome.
Upon request, a wireless connection system can be provided.
The towers are CE marked according to Directive 89/106 of 21/12/1988.
All steel components making up the lighting towers are hot-dip galvanized by immersion in a zinc bath, in accordance with UNI EN ISO 1461 standards.
Upon customer request, powder coating is available, carried out in compliance with UNI EN ISO 2409, class 1-2808 – DIN 53132 – ASTM B117.
The development of communications has made it necessary to use antenna-supporting structures capable of transmitting signals even in the most remote areas. For this purpose, N.C.M. offers an economical and safe product that meets the most diverse needs.
This solution allows for reduced installation times and lower environmental impact, with significantly lower costs compared to traditional lattice structures.
The types of telecommunication towers can be as follows:
Monotubular towers, equipped with ladders and cable-support brackets, used for installing antennas along the shaft.
Monotubular towers equipped with ladders, cable-support brackets, and a maintenance platform at the top, complete with all the equipment needed for antenna installation.
Monotubular towers with a mobile crown at the top to support lighting projectors and a flagpole for antenna mounting.
They have a tapered polygonal cross-section and are made by press-bending and subsequently welding trapezoidal steel sheets of grade S355JR (in accordance with UNI EN 10025 standard).
The towers consist of multiple sections, the number of which varies depending on the total height, joined using the slip-on joint method.
The towers can either be: directly embedded in the ground via a concrete foundation base, or, if equipped with a base plate, anchored to the foundation using embedded bolts.
All welding is carried out using a procedure certified by the Italian Welding Institute, performed by qualified personnel and tested in compliance with UNI EN 3834-2 standard.
The structures are CE marked and manufactured in compliance with UNI EN 1090 standards, with an execution class of EXC 2.
The high masts are hot-dip galvanized by immersion in a zinc bath in accordance with UNI EN ISO 1461 standard.
Upon customer request, powder coating is available, executed according to UNI EN ISO 2409, class 1-2808 standards.
Work platform with a rectangular or square shape, complete with anti-slip grating flooring, toe board, protective handrail with a height of 1.2 meters, intermediate knee rail, and access hatch.